Plastic Film Extrusion - Packaging
" ... what is it that really makes us unique in film extrusion?..."
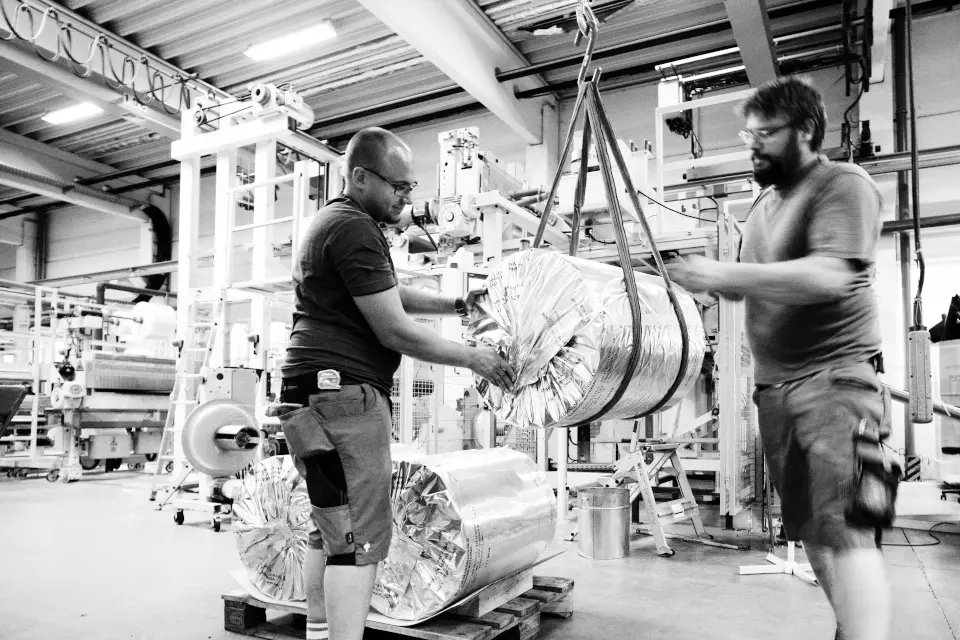
"... it is the development, optimization and manufacture of plastic films that are precisely tailored to the respective application. Sometimes the customer himself is involved, experimenting and sampling. At others, he has to take what he gets as standard. We talk about what his product really has to be able to do, and how we achieve that. Thinking in terms of raw material cycles and including secondary raw materials is increasingly becoming the focus of our consideration ... "
On our 4 extrusion lines, we extrude films in thicknesses ranging from 0.100 to 2.5 mm and in possible widths from 350 to 1000 mm. We offer monofilms as well as multi-layer structures, matt surfaces using rubber rollers as well as highly transparent surfaces using smoothing machines. Packaging films, inline as well as offline into narrow cuts or formats is also part of our capabilities. We offer pretreatment of films (corona) as well as inline lamination onto various substrates (nonwovens, decors, protective films). We have already had the opportunity to gain experience in the processing of numerous materials. We currently work regularly with thermoplastic polyurethane, conductive polystyrene, impact-resistant polystyrene, ABS, polyamide, polycarbonate, PET-G, renewable raw materials, secondary raw materials... Sometimes, however, customers come to us with finished formulations and compounds, which we then extrude for them.
One thing in advance ... technical films made from secondary raw materials are not "cheap and inferior recycled films", and projects in this regard are not a continuation of familiar thought patterns.
Rather, it is a matter of gradually moving away from a linear economy with all its mountains of waste, toward narrow minded thinking and the view that "waste" can in many cases be valuable raw materials again. This requires a completely new mindset. It is about looking at the entire value chain and the entire product life cycle. It is also sometimes a matter of contrasting what circularity requires with previous product properties and asking whether, on closer examination, these properties are not sometimes believed to be necessary properties which, in the end, do not bring any really significant use in the application and, from today's point of view, are no longer sustainable in the light of the necessary circularity thinking. As plastic solution finders, we are used to ambiguous and contradictory tasks. A good prerequisite for the characteristics of closed-loop projects, we think.
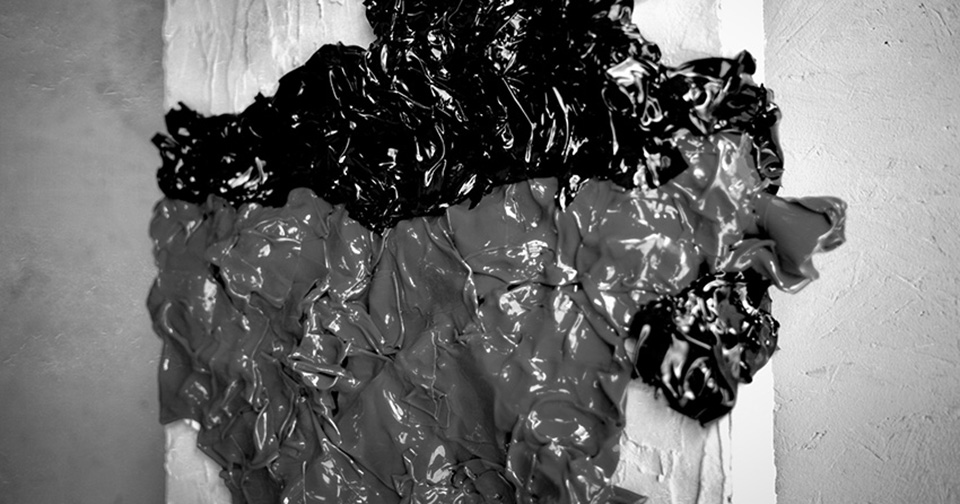
Films from secondary raw materials
Foil types
We produce the adjacent technical slide groups on a regular basis. If what you need is not there, please contact us anyway. We will then clarify together whether we can offer a manufacturing option.
"Realized Extrusions Project Examples"
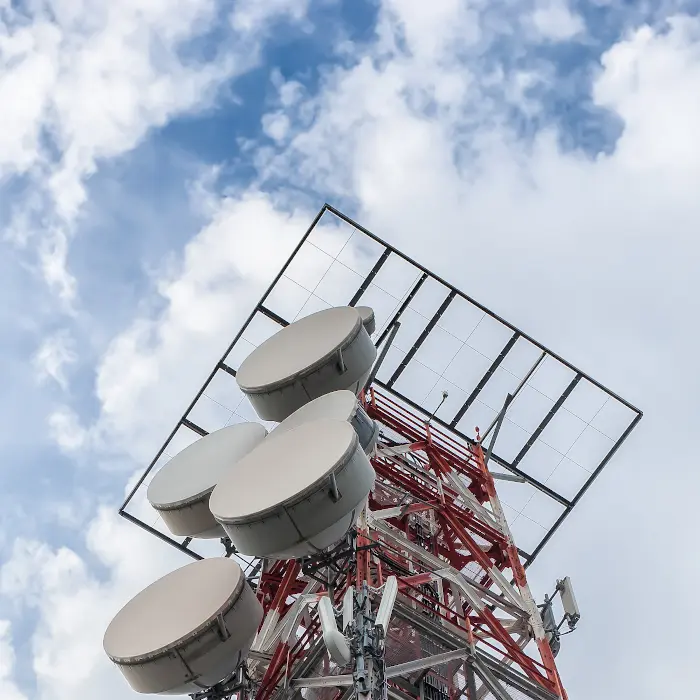
Antennas foils
The specially developed PC - foil composite protects the antennas from wind and weather. On the one hand, the structure of the film meets the high requirements for weather resistance and, on the other hand, it has been optimized for further processing. This saves time-consuming steps in the production process. Of course, the influence on the transmitting frequencies is minimized, which is also facilitated by the individually adjustable foil thickness.
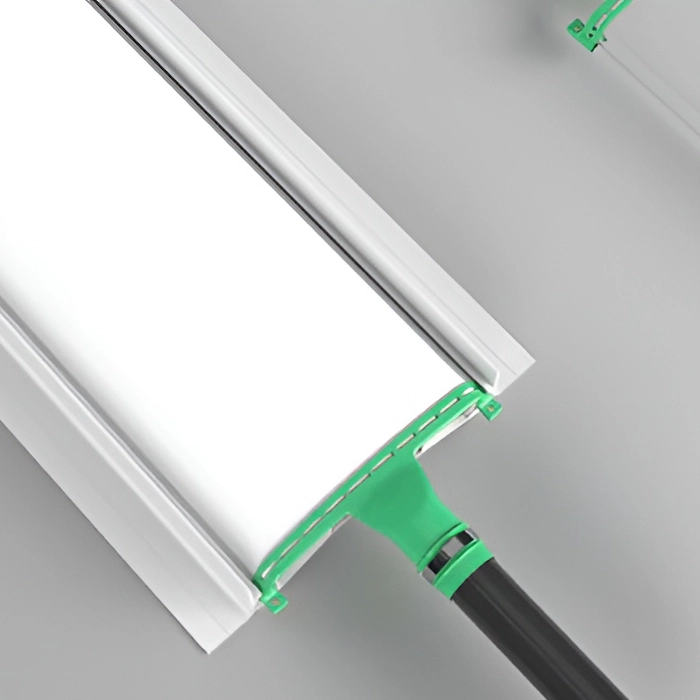
Jäger Umwelttechnik - Waste water aerator
A few years ago, the company Jäger Umwelttechnik approached us with an idea ... The goal is to ventilate wastewater with the help of a flat hose made of thermoplastic polyurethane... since the first thought is about an extruded profile, we would not have been the right partner in a superficial view... but as a plastic solution finder we looked at this requirement from a different perspective and developed and implemented a product ready for series production together with one of our welding partner companies ...
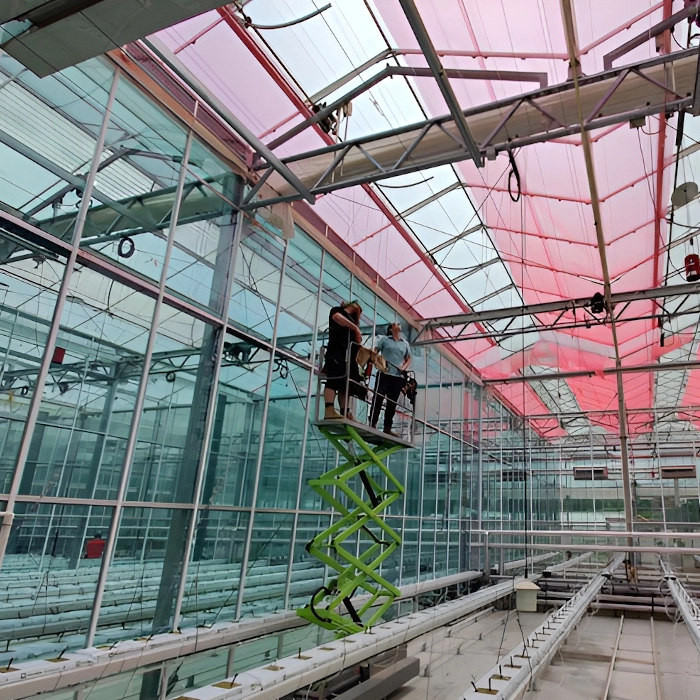
LLeaf - film for improved plant growth
Together with the company LLEAF, a film project was launched for the European market, in which the growth of plants can be accelerated. The color developed by LLEAF is combined with our durable PC film. When the light shines through this film, the color spectrum is changed in such a way that it supports the growth of the film enormously. This helps to make better use of the resources currently used (earth, space, energy) and also to dispense with or reduce artificial light.