CONEXUS – new KTM technology with Filzwieser film
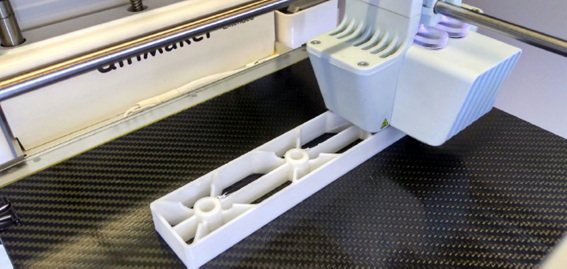
As part of the Engel Mobility Day, KTM Technologies presented a groundbreaking technology that addresses the central themes of the event – sustainability and progress through technology. The innovative CONEXUS connection technology was developed by Filzwieser in the field of film extrusion of the compound layer supports and enables the production of extremely strong bonds between fiber composites and thermoplastic materials. This revolutionary development opens up completely new possibilities for combining and advancing the advantages of both material worlds. A decisive step in this process is the integration of a flexible film from Filzwieser in the production process of composite fiber parts. This makes it possible to create components with high stability and temperature resistance that also have integrated connection options such as snap-in hooks or overmolded screw bushings. This leads to the elimination of conventional connection techniques such as screwing or gluing. The absence of bonding in particular significantly improves the recyclability of the components. A successfully implemented series project at KTM is the brake disc cover of a motocross machine, which is manufactured using CONEXUS connection technology. This revolutionary solution makes it possible to create high-strength bonds between carbon fiber materials and easily processable polyamide plastics. This component was thus significantly increased in terms of rigidity and temperature resistance, while the weight of the component was reduced.
CONEXUS connection technology offers numerous advantages, among them:
- Mass production
- Easy separation of the two materials (recyclability)
- High reproducibility and surface quality
- Integration of functions while reducing process steps
- Cost and weight reduction
The continuous development and application of CONEXUS connection technology promises an exciting future in the production of hybrid components. The combination of high-strength fiber composites and easily processable thermoplastic materials opens up new perspectives for sustainable and advanced solutions in various industries. Finally, one example is direct 3D printing on CFRP components.